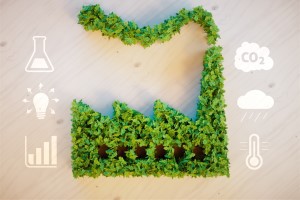
Energy is at the heart of our industrial society and it is no surprise that a majority comes from fossil energy (80% of the world’s consumption is attributed to oil, gas, and coal). For example, in one day, the world uses the equivalent 15 billion barrels. While most of the oil is consumed in engines (cars, trucks, boats, trains, airplanes), a portion is used for packaging production, cosmetics, textiles, and food production. The consumer goods industry is very energy-intensive, as it is used at many points throughout the product life cycle (supply, production, packaging, distribution, consumption).
Energy in the food and cosmetics industries
A product life cycle, including manufacturing, distribution, consumption and processing, whether in both food and beverage and cosmetic industries involves multiple energy consumption points including oil, electricity and gas: transportation (in the US, it represents 14% of the energy used in food production), factories that need to keep running, refrigeration systems, etc. The list is long! In addition, oil is found in cosmetics as an ingredient (e.g. paraffin, Vaseline, hair lotions, etc.). As for the food industry, which is the 3rd most energy-consuming industrial sector after the chemical and metallurgical industries, it is important to consider energy consumption during the production of raw materials. The agricultural part alone accounts for 20% of the total energy of the sector, due to equipment and vehicles for harvesting, livestock farming, etc. To give you an idea, the energy needed to deliver 1 Joule in the form of food requires almost 10J of natural resource energy.
So, oil is largely used in the production of goods from the CPG manufacturers. But its global production decline has sparked an urgent need to rethink the system to reduce the need for fossil fuels.
Actions at every step of the life cycle
Actions have already been put in place by food companies, notably the use of renewable energy. They have started using biofuels or producing raw materials to develop biofuels. A typical example is the use of bagasse as a biofuel to generate the energy needed for processing in sugar farms. It is therefore quite possible to optimize current uses and also find new solutions. As for the cosmetics industry, there has been a shift toward vegetable oils, like olive or coconut oils.
If we follow the life cycle of food products, we can find areas of improvement at every stage. First, we can cite innovative farming techniques such as the improvement of irrigation systems and the development of so-called precision farming (optimization of yields and investments, taking into account the variability of environments and conditions between different plots as well as at intra-parcellar scales.) Secondly, let us remember the importance of local production and consumption which contribute to reducing transportation. Third, energy savings can be made in the development of eco-responsible packaging using reusable materials. Finally, the impact of the use of more energy efficient appliances, machinery, processes and even buildings throughout the supply chain should not be underestimated.
The contribution of PLM
More and more companies are moving to green manufacturing of products to minimize the use of natural resources and reduce emissions of pollutants.
Bringing together all the information on design, production, and sales processes in a single repository, the PLM helps companies to make informed decisions at every stage of development. Raw materials, supplier work practices, packaging recyclability, production process, everything is documented which allows to monitor every aspect of the product life cycle. Using metrics and comparisons, energy consumption can be modeled in the PLM to achieve sustainability goals. For example, it is possible to compare two suppliers according to the amount of fossil energy needed to transport raw materials. The PLM can also simulate the amount of electricity needed to make the product (manufacturing process, refrigerated storage, etc.). By introducing and tracking “sustainable” indicators, companies using a PLM can simulate in real-time the amount of energy used throughout a product’s lifecycle. Thus, they can correct it or set up continuous improvement processes and develop greener products.