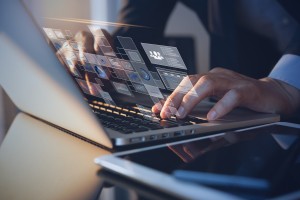
A PLM (Product Lifecycle Management) system is a collaborative tool allowing to manage the entire product lifecycle of a manufactured product. It gathers in a unique and central repository all product-related data and eases communication among actors involved in the development process.
Key functionalities
PLM systems originally come from the Discrete Manufacturing Industries, mainly aeronautics, defense and automotive manufacturing industries. The main purpose was to identify the multitude of components during the three phases of a product’s life: the design/ as designed, the production / as-built, the maintenance / as maintained. Nowadays PLM’s influence grew to reach Process Manufacturing Industries like Consumer Packaged Goods (CPG). Indeed, in the very competitive and regulated CPG industries, a PLM system can provide a competitive advantage with today’s market pressures to lower costs, improve quality, and reduce the time to market.
Any PLM supplier, no matter the industry, should make sure its solution provides, in addition to a data and document repository:
- A workflow/process engine: to ensure data sharing and collaboration between every actor involved.
- A change management tool: to ensure that any product change is stored and its global impact is evaluated.
- A supplier management tool: to help companies to find the best suppliers and ease collaboration with them to complete the raw materials and packaging database.
- A reporting tool: to help to synthesize data and help managers to make the right decisions.
Key advantages
With a PLM, product development teams can leave their independent systems (separated Excels and database, emails, etc.) and work on the same platform. This allows to considerably reduce the risk of data loss or miscommunications. A PLM also allows better traceability by providing tools that manage product-related data and documents, by tracking all product modifications and controlling processes of approval. Suppliers become assets thanks to an easier collaboration. They can autonomously fill their information in a portal, so it eases analysis and facilitates the choice of the right supplier. By helping to synthesize data, create a customizable dashboard based on chosen KPI (Key Performance Indicators), PLM allows to monitor any project in real-time, and facilitate decision making.
By managing all steps of product development processes and storing all data or documents, PLM brings more efficiency and transparency. This leads to lower costs, shorter development time, and allow the organization to capitalize on information.
Which PLM for which industry?
If any company involved in product development can use a PLM system, it does not mean that every firm will use the same one. On the other hand, to be helpful, a PLM needs to be tailored for the industry it will work in. Why? Well, because all industries do not face the same challenges. CPG industries need to meet strong consumer demand for transparency, traceability, and sustainability and therefore accelerate innovation while meeting regulatory requirements and ensure consumer safety. All of that with sometimes only a few weeks between the brief and the manufacturing. Even if regulations and consumer safety are also matters to be addressed, DMS industries face challenges like long-term change management or over adaptation to a customer-specific need.
So, it is essential for a PLM to be designed specifically for the industry it will work for. For example, for DMS industries, it needs to be combined with a CAD tool. It will gather all the information in the same place and so minimize errors and reduce tasks without value. With the two solutions well integrated, changes made in the CAD solution will be automatically updated in the PLM system. A parallel can be made with the formulation tool in process industries like Food and Beverage and Cosmetics and Personal Care. It automatically calculates the impact of any change made in the formula or the recipe.
A PLM system also allows standardizing processes. But, if in DMS industries processes are strict – as the process required to change a screw-type on a part of an aircraft – and time to market are long (there are at least 5 years of test for a plane), in CPG industries, due to the challenge of shortening time-to-market, processes, and therefore PLM must be flexible to let teams react quickly as business needs evolve. For example, you must sometimes launch the production even if everyone has not approved yet. The PLM should allow you to take the risk even if it means trashing the produced product if there is a problem afterward. Another aspect is that, in the CPG industry, PLM technology is used by a wide range of different teams (marketing, design, R&D, etc.). In DMS, it is mainly used by technicians who are used to working with technical software. Solutions in CPG industries, therefore, need to be easier to use and aesthetical as teams are more sensible to ergonomics.
Any company, independently of its size, developing products can benefit from a PLM system because it simplifies and shortens each phase of the product development process. The challenge is to choose the right one for your company.