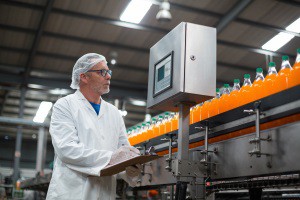
Determining the product’s consistency and conformity, the batch sheet counts as one of the most critical documents of the product lifecycle.
Errors in the batch sheet may result in non-compliant products towards quality or regulatory requirements, cross-contamination on the production line, etc., which can lead to a dead loss of production time and materials or customer health incidents in the worst-case scenario.
Whereas solutions to edit batch sheets are well known for most of manufacturers, we tend to forget why they were created and where the errors they are designed to prevent come from. So, let us look at the major pain points that can lead to corrupted batch sheets.
Failing batch sheets with inaccurate input data
Generating the batch sheet consists in a delicate compilation of data, not much more. On one hand, this limits the number of potential ways to make mistakes. On the other hand, it makes batch sheets highly dependent on the quality of the base data.
Today, are you able to answer these questions:
- Are all the productions facilities’ details correct?
- I am editing the batch sheet. Are the product specifications I use approved?
- Am I filling the last up to date template for the batch sheet?
Failing batch sheets because of data manipulation errors
When performed by a human being, every calculation or manipulation of data is error prone. As simple as the operation can be, even the best mathematician can misreport its results.
This can happen multiple times during the batch sheet generation when:
- scaling up the net quantities of raw materials
- retrieving the details of the production capacities: equipment on the line, available raw materials, batch size, etc.
- writing the manufacturing process and mistakenly capturing components, quantities, tools or instructions
Aptean PLM Lascom Edition solution for batch sheet generation
Our 7 commandments for data management are:
- Dematerialize to homogenize the data
- Centralize to consolidate the company’s knowledge
- Structure to ease the research of information
- Secure to guarantee reliability of data
- Share to improve collaboration throughout the NPD (New Product Development) process
- Track to avoid any data loss and to capitalize on all past projects
- Automate operations to eradicate human errors and free teams from tasks with no added value
All of these conjointly vouch for a “unique version of the truth” throughout the NPD process, from the marketing brief to the batch sheet. Lascom’s PLM software does all of that (and even more). At the end of the line, just before generating the batch sheets, you are assured to have approved and up to date:
- Raw material specifications
- Packaging specifications
- Finished product specifications
- Supplier details
- Production details
Our solution then retrieves the data required to fill the batch sheet template you pre-defined and automatically generates it. Your teams save a considerable amount of time, drastically reduce errors and, overall, reduces your time-to-production and strengthen your customers’ fidelity if you are a contract manufacturer. Our different modules for food and beverage and cosmetic and personal care manufacturers come in two standardized packages, “Essential” and “Corporate“, to bring the power of PLM within everyone’s reach!