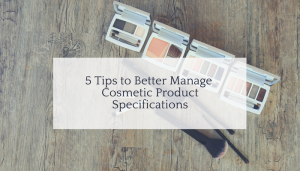
Every new product comes with its specification that defines its identity and characteristics for both internal and external use. Often, people expect it to be one document including all the needed information but it is more complex than that. The product specification is a dossier that gathers many documents and data from different stakeholders, both internal and external. The dossier is created and updated by all the company departments during the new product development process and for its entire lifecycle.
Cosmetic product specifications: what is included?
- Product identity: the exact name, identification code, weight, manufacturer name and address, etc.
- Product characteristics:
- Raw material composition
- Quali/Quanti formula : INCI ingredients list and raw materials
- Physical/chemical characteristics and stability of the product
- Microbiological quality
- Impurities, traces, information about the packaging
- Exposure to the product, to the substances
- Test and toxicological profile report
- Undesirable and serious effects
- Statement on the safety of the cosmetic product
- Instructions of use
- Safety data sheets of raw materials
- Manufacturing process
- Evidence of the claimed effect of the cosmetic product
- Cosmetic product labeling
The complexity of cosmetic product specifications management
To get the detailed product specifications data and documents must be gathered from different departments within the company but also from many suppliers. Collect information from different sources is time consuming and difficult to manage as everyone is working on different type of document and templates – excel sheet, own template document, etc. Working on multiple documents can also means difficulty to keep tracks and updates. Every department need to access it but not necessarily at the same time and most of the time not to collect the same information.
All these documents must be accurate and maintained updated for the entire product lifecycle. All product change, even after its launch, will have an impact on product specifications. It could be product formulation change, regulations evolution, raw material increase, etc.
In addition, during the product development process, data and documents are not accessible at the same time, as some information will be available only after a certain stage has been completed. For example, the formulation and exact composition of the product is accessible only when formulators have defined and approved it.
Product specifications also means tasks synchronization between the company departments. They do not work on the same stage of the process but they need each other to move forward. Packaging teams need information from formulators and compliance. Product development need document from marketing, compliance, packaging and quality teams. They all have to be synchronized with each other to work efficiently.
5 best practices to manage cosmetic product specifications
To better manage product specifications, you also need to manage raw material and packaging specifications as they both have an impact on the finished product specifications. Every raw material is composed by several ingredients, documents and data. And that can easily lead to hundreds of documents and data to manage at once. Centralize and update them in a unique source will considerably help tracking and sharing.
1. Create a raw material specifications database
All information related to raw materials must be centralized in a unique database. That includes information about ingredients, suppliers, required document such as the Safety Data Sheets, manufacturing processes, classification, etc. Collect and update product specification will be quicker and easier as everything will be found at the same place.
2. Create a packaging specifications database
In addition to the raw materials specifications, and to compile product specifications, you need to gather all information related to the packaging. Including information from the supplier, costs, technical characteristics, prototypes, etc. All of these documents and information must be gathered at the same place than any other information regarding product specifications.
3. Structure information related to product specifications
After collecting and centralizing all the data and documents regarding product specifications, everything should be structured and organized. It will help to save time, increase team efficiency and enhance collaboration. Based on product specifications’ requirements, you need to create pre-defined templates per product category. Having templates will facilitate information access and organization as everyone will have to follow the same frame based on the needs. No more information missing, human errors or dozens of hours wasted to look for the right information.
4. Implement workflows to manage teams’ tasks
In order to ensure each stage is respected and information is accessible immediately, workflows can make a huge difference. As mentioned earlier, some information are not available until a task is finished. With a workflow, you’ll have the ability to assign a task and send alerts when the task is complete. For example, as soon as the R&D have finished the cosmetic formulation, regulatory affairs need to check composition compliance. With a workflow, they could receive automated notifications and direct access to the right information. Collaboration and sharing between departments is then made easier.
5. Create templates for reports
When you have collected, checked and centralized product specifications’ data and documents in an structured way you’ll be able to generate reports for both internal and external use. The product specifications report will be the final dossier sent to give more details about the product and its composition. It can be use in stores to give customers more transparency or internally to create similar products. To simplify this process, you must create templates with the required information so that you will be able to automate its creation when needed. Template can be customized depending on the need and reader.
Managing product specifications can be very complex but is key when developing a new product for either the development phase but also after product launch. Lascom Product Lifecycle Management software has been developed to manage your product specifications and on an efficient and optimized way. Collect, check, share and update each specifications easily and quickly.